Robotized system for welding in structural steel fabrication
1/10/2015 – 1/04/2017
CoopWeld’ system addresses specific SME needs and by its characteristics will be the 1st system dedicated to the automatic welding of metallic structures in SME. CoopWeld’ system will be the outcome of combining the FP7 SMERobotics Clarissa project results with the augmented reality technology “projection mapping”, and will be a cooperative system where the robot carries out the less valued and more time consuming tasks and the system operator is responsible for the mounting operations, aided by the augmented reality system that is mounted in the robot. The project will also develop intuitive tools to support decision making at the welding level which will facilitate the system operation and contribute to its productivity and quality. Project consortium joins 3 members coming from the FP7 SMERobotics Clarissa project, which are a software developer, an end-user and a research center in robotics and an entity from the Scientific and Technological system whose expertise is welding. The 4 entities own the required competencies for developing the innovative CoopWeld system, which is believed to significantly impact the metallic structure fabrication segment which is mainly dominated by SME.
The objective of this project is to demonstrate, in an industrial environment, a robotic solution applied to the welding of metallic structures for the construction industry. This cell results from a detailed analysis of the needs of the SMEs and thus an easy to operate and maintain equipment. The objectives can be summarised as follows:
1. Development of a robotic cell with an estimated production capacity of 15,000 ton/year;
2. Reduction of 50% of the welding cos;
3. Development of an equipment adaptable to the reality of SMEs, with reduced deployment space, affordable acquisition and maintenance costs and reduced return period of investment, less than 3.5 years.
To achieve the objectives described above the CoopWeld project proposes the development of a collaborative robot with the following characteristics:
1. Complete integration of design information (CAD) for automation of the welding process;
2. Human-machine cooperation through the projection of digital information on the structure to be assembled, which when compared to the most current methodology (assembly with tape measure and chalk / scratch) gives the operator greater ease and speed of assembly with a high degree of precision;
3. Reduced impact on factory layout through advanced sensor integration in the sharing of space between operator and robot.
Contact: Germano Veiga
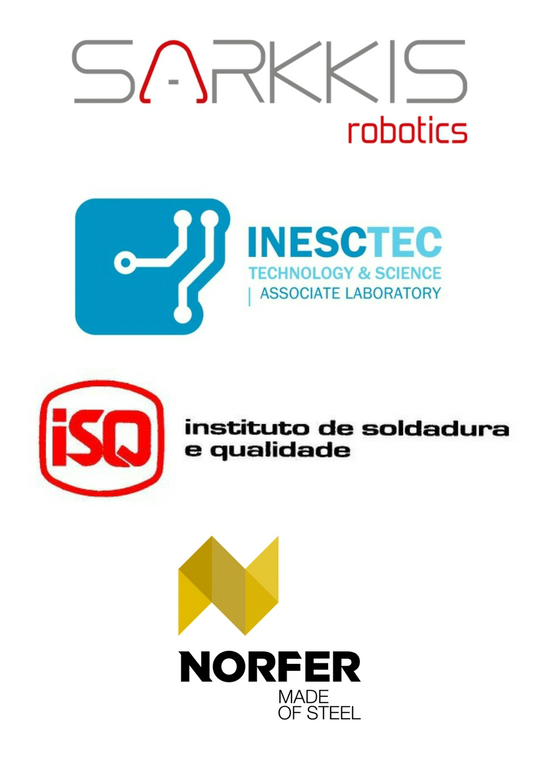